INDUSTRY: Mining, Aggregates, Recycle
material type: Hard Rock, Concrete & Asphalt
Wheeled Jaw Plant Model
3055j-w
With an impressive opposing wedge design, the 3055j-w jaw crushing plant is perfectly suited for any-size job. Lippmann has engineered the chassis to accept any application you require, including a hydraulic hopper removal system, extended discharge conveyor to feed secondary or screen plant, diesel or electric, hydraulic dump grizzly, cross conveyor, and hydraulically folding hopper extensions.
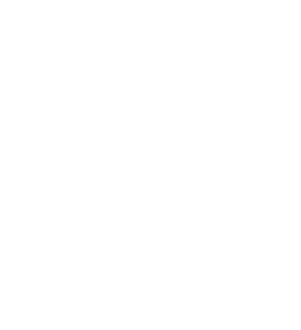
Highlights
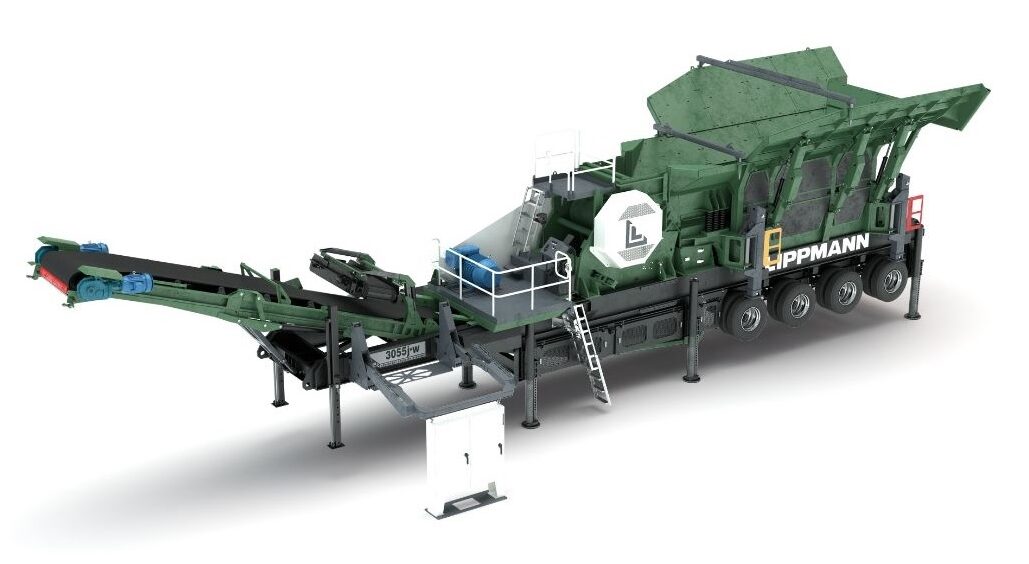
54" (1372mm) Conveyor with CEMA C idlers,
premium belt scraper, and extended
with a hydraulic fold
Optional: hydraulically removable
control panel
Adjustable tail section
Optional: jack legs,
(4) hydraulic leveling jacks or
(6) run-on jack legs
30" (762mm) gape by 55" (1397mm) wide
jaw with opposing wedge design
Optional: grizzly bypass
discharge conveyor
55" (1397mm) by 20' (6.10m) vibrating
grizzly feeder with 5' (1.50m)
adjustable grizzly section
Wedge adjustment
20-ton (18ft) hopper constructed
of AR steel
The Lippmann Edge
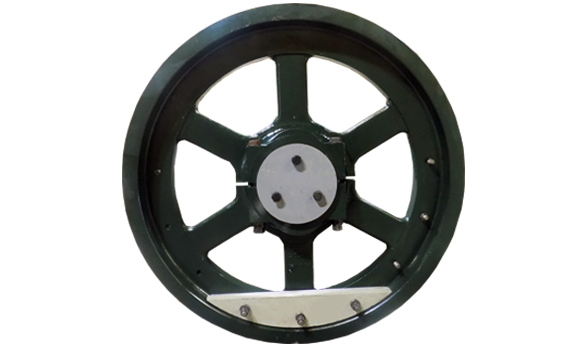
Oversized Shaft, Dynamically Balanced Flywheels
All Lippmann heavy-duty jaw crushers feature an oversized, heat treated shaft forged of special alloy to provide an exceptionally large eccentric throw. These heavy-duty shafts are paired with two dynamically balanced flywheels, effectively reducing vibration on both portable and stationary crushers. The overhead eccentric configuration does not rely on gravity alone to move material through the chamber. Rather, the inward and downward movement of the swing jaw provides for a forced-feeding motion to maximize output. All shafts are machined and put through a rigorous inspection process before they enter production.
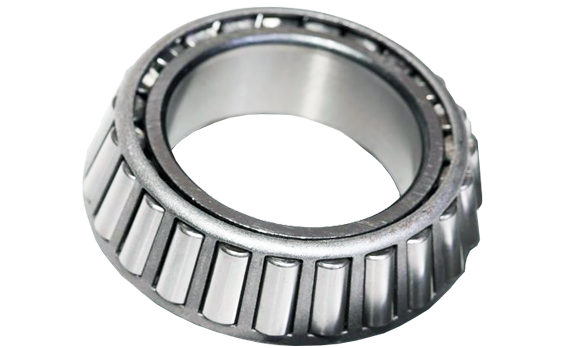
Tapered Roller Bearing for Optimized Bearing Life
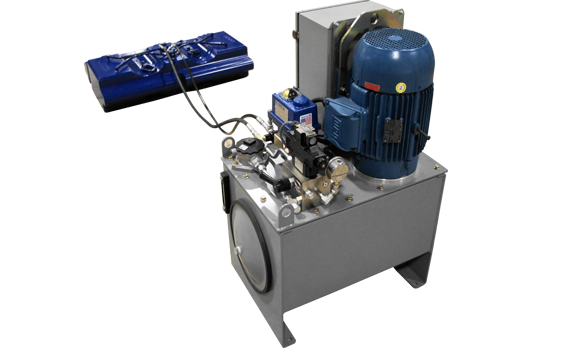
Hydraulic Toggle Reduces Setting Time
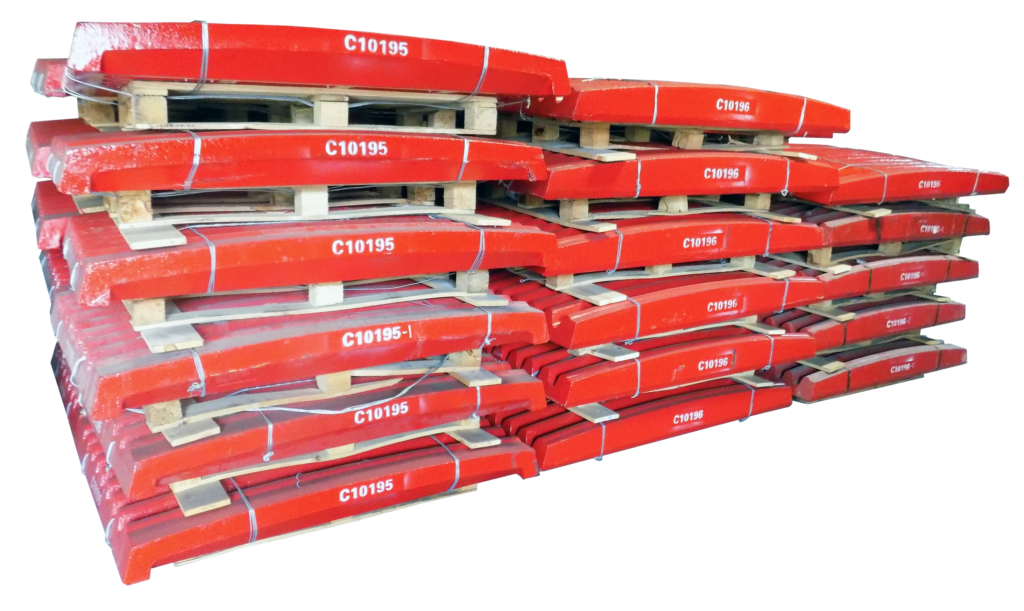
Reversible Jaw Dies for Longer Life
All standard Lippmann jaw dies (stationary and moving) are reversible. They can be flipped from end to end as necessary to get better lifespan out of them. The corrugated design that is centered about the jaw crusher allows this. Lippmann uses a peak to valley arrangement to break the rocks, using shear rather than direct compression.
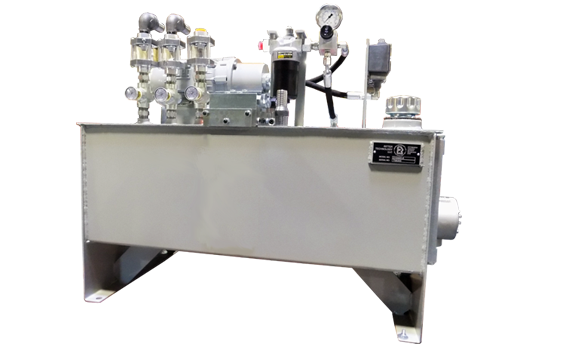
Oil-Bath Lubrication System
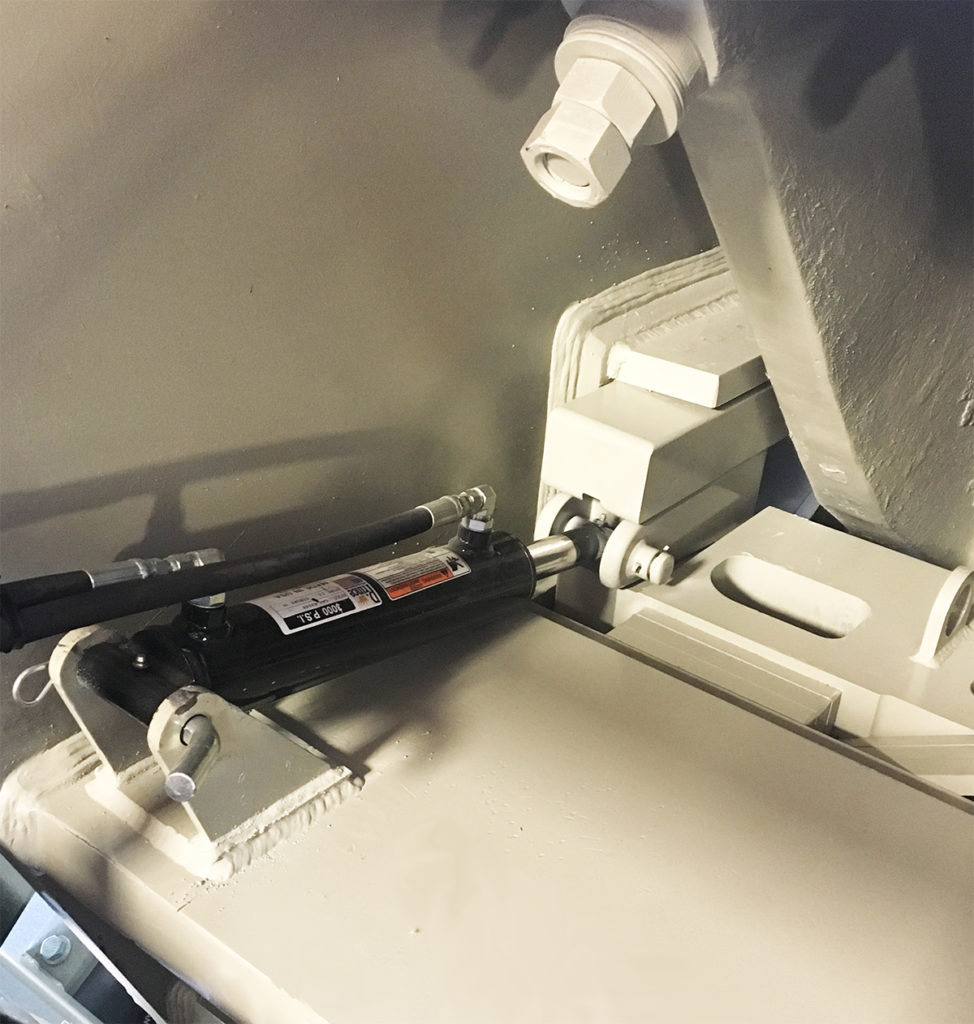
Taper Lock
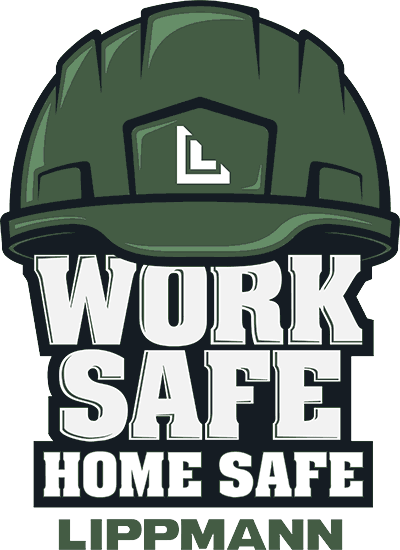
Safety at Every Step
Standard Features & Options
Standard Features
- Extra-heavy ribbed steel frame is stress-relieved after welding and before machining
- One-piece steel pitman
- Heat-treated forged alloy steel eccentric shaft
- Oversized roller bearings on the pitman
- Spherical roller bearings on the frame
- Reversible manganese steel jaw dies and extension
- Steel cheek plates
- Opposing wedge toggle tensioning system
- Grease-lubricated
- Two heavy-duty flywheels, one grooved for V-belts
Options
- Hydraulic leveling jacks – (4) 70,000 lbs (31,752kgs) or (6) Run-on jack legs
- 12-motor control center
- Cross conveyor under grizzly
- Hydraulic folding hopper extensions
Technical Specs
3055j-w SPECIFICATIONS | ||
---|---|---|
US | METRIC | |
Jaw Crushers | 30″ x 55″ | 762 x 1397mm |
RPM | 250 rpm | 250 rpm |
Stroke | 3/4″ | 19mm |
Feed Size | 27″ | 686mm |
Discharge Conveyor | 54″ | 1372mm |
Discharge Conveyor Operating Speed | 318 hp | 237kw |
Feeder | 55″ x 20′ | 1397mm x 6.10m |
Feeder Operating Speed – Max | 830 rpm | 830 rpm |
Grizzly Length | 5′ | 1.52m |
CLOSED SIDE SETTING (CSS) | |||
---|---|---|---|
INCHES | MM | STPH | MTPH |
3 | 76 | 250 | 227 |
3.5 | 88 | 288 | 261 |
4 | 102 | 345 | 313 |
4.5 | 114 | 400 | 363 |
5 | 127 | 420 | 381 |
6 | 152 | 500 | 454 |
7 | 178 | 600 | 544 |
8* | 203* | 720 | 653 |
*Manual toggle plate option only
Hydraulic toggle or manual toggle plate available
HORSEPOWER | ||
---|---|---|
HP | KW | |
Jaw Crusher | 200 | 149 |
Autolube | 1 | 0.75 |
Opposing Wedge | 1 | 0.75 |
Feeder | 40 | 30 |
Discharge Conveyor x2 | 15 | 11 |
TRANSPORTATION | ||
---|---|---|
LBS | KGS | |
Tires | 315/80R22.5 | 315/80R22.5 |
Rear Axle | 71,000 | 32,201 |
King Pin | 55,750 | 25,288 |
TOTAL | 126,750 | 57,493 |
Weight of Feeder Module | 69,250 | 31,411 |
TOTAL WEIGHT | 166,250 | 75,410 |
Lippmann reserves the right to make changes to the information and design of the machines on this website without reservation and notification to the users. Information at time of publication is considered accurate – Lippmann assumes no liability resulting from errors or omissions in this document.