INDUSTRY: Aggregate, Recycle
material type: Limestone, Gravel, concrete, asphalt
Closed-Circuit Impactor Plant
4800r Closed-Circuit Impactor Plant
With 6 run-on jack legs, this self-contained and closed-circuit plant is ideal for quick recycling runs. An effective rear-discharge lets material naturally flow through the impactor, onto a pan feeder, and then into the conveyor belt while a cross-belt magnet helps eliminate steel and any other potential tramp. And now with an upgraded 6×14′ screen, the 4800R plant is ready to reach its true potential on your job site.
The 4800R features were engineered using information from our customer base and dealer network, delivering a closed-circuit impactor plant a step above the rest.
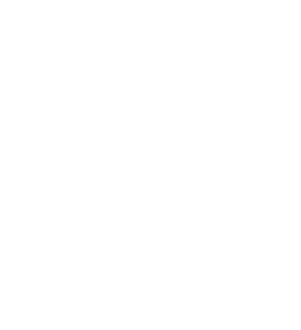
Highlights
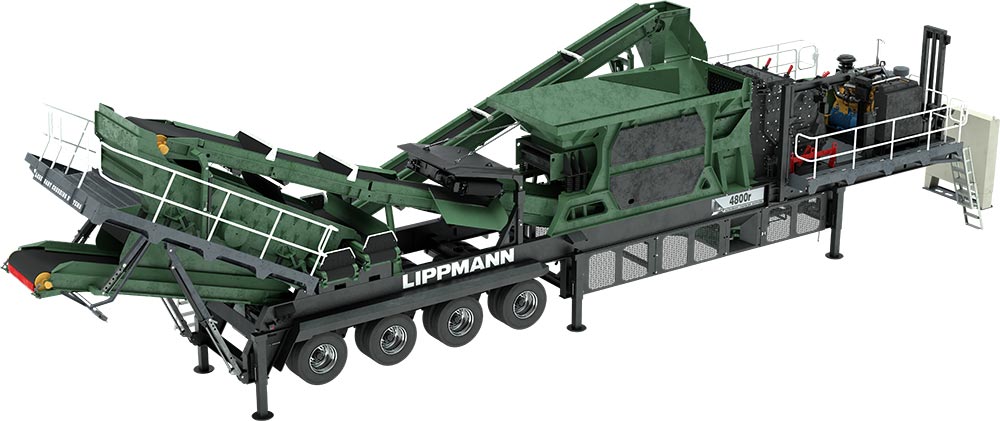
Hydraulically adjustable cross-belt magnet eliminates rebar and foreign material
Cleated return conveyor belt
Industry’s lowest return conveyor angle
reduces rollback and optimizes feed angle
Overflow to bypass chute prevents
buildup or spillage
3- and 4-bar rotor options with crushing
chamber improve material flow efficiency
Spacious underpan area allows
smooth and consistent material flow
Dust suppression at impactor
feed as standard
(6) Hydraulic run-on jack legs
Easy to remove reversible cross conveyors
Hydraulically adjustable discharge conveyor angle
Hydraulically removable electrical panel
for easy set up and reduced vibration
The Lippmann Edge
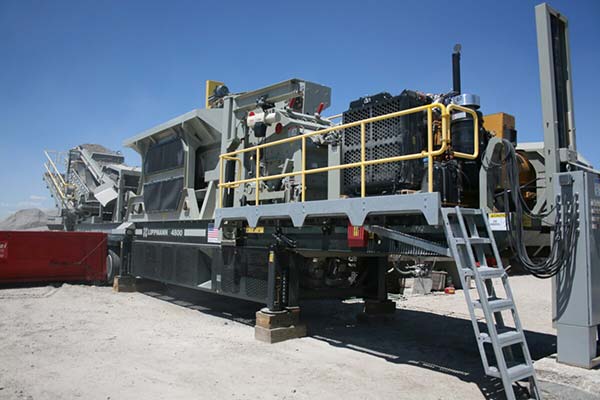
This self-contained impactor plant is equipped with a direct drive 415hp (310kW), Tier 4 Final engine.
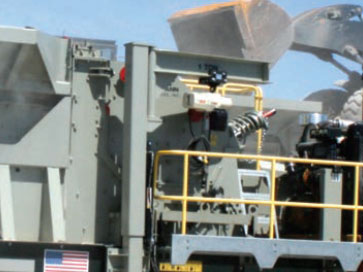
On-board jib crane simplifies blow bar replacement process for ease of maintenance.
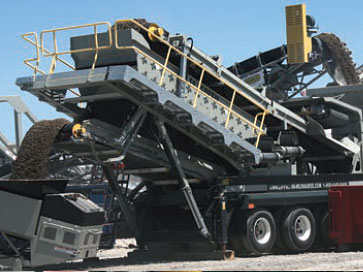
Hydraulic Toggle Reduces Setting Time
Hydraulically adjustable screen angle allows you to select the appropriate angle for your application. The spreader split ensure material is evenly deposited on the vibrating screen.
Recirculating material flow
Recirculating material flow
Standard Features & Options
Standard Features
- Andreas-type impact crusher design
- Highly cubical product
- High ratio of reduction
- Hammers have four crushing positions to maintain a more consistent gradation and greater top size control
- No weld build-up required
- One gravity and one spring loaded curtain
- Inspection door on side of machine
- (6) Run-on jack legs
- NEMA 12-motor control center
- Tire bulkheads
Safety Features
- Fully guarded moving components (drive belts, etc.)
- Controls located safe distance from moving component
- Stationary access point to screen walkway
Options
- Diesel or electric drive
- Asphalt or recycling setup
- Feeder finger spacing options 1-1/2″ or 3″
- Feeder Grizzly bar 1-1/2″ or 2-1/2″
- 315 tires
Technical Specs
CRUSHING CHAMBER, FEEDER & SCREEN | ||
---|---|---|
US | METRIC | |
Impactor | 42″ x 48″ | 1067 x 1219mm |
Impactor Operating Speed | 600/630 RPM (option dependent, rock/asphalt) | 8.67Hz |
Feeder Size | 192″ x 47″ | 4877 x 1194mm |
Pan Feeder | 48″ x 72″ | 1219 x 1829mm |
Screen Size | 168″ x 72″ | 4267 x 1829mm |
Number of Decks | 2 | 2 |
Screen Speed | 20HP | 14.9kW |
CAPACITY | |||||
---|---|---|---|---|---|
MATERIAL | SETTING | CAPACITY | MAXIMUM FEED SIZE | ||
IN | MM | TONS | IN | CM | |
Limestone | |||||
1.75 | 44 | 170-225 | 16 | 41 | |
2 | 51 | 175-230 | 18 | 46 | |
2.5 | 64 | 180-240 | 18 | 46 | |
3 | 76 | 190-260 | 18 | 46 | |
Gravel | |||||
1.75 | 44 | 170-225 | 6 | 15 | |
2 | 51 | 175-230 | 8 | 20 | |
2.5 | 64 | 180-240 | 8 | 20 | |
3 | 76 | 190-260 | 8 | 20 | |
Concrete | |||||
1.75 | 44 | 170-225 | 16 | 41 | |
2 | 51 | 175-230 | 20 | 51 | |
2.5 | 64 | 180-240 | 20 | 51 | |
3 | 76 | 190-260 | 20 | 51 | |
Asphalt | |||||
1.75 | 44 | 170-225 | 28 | 71 | |
2 | 51 | 175-230 | 28 | 71 | |
2.5 | 64 | 180-240 | 28 | 71 | |
3 | 76 | 190-260 | 28 | 71 |
Secondary apron to hammer tip clearance in inches and cm
CONVEYORS | ||
---|---|---|
US | METRIC | |
Discharge Conveyor | 190″ x 40″ | 4826 x 1219mm |
Discharge Conveyor Operating Speed | 310 ft/min | 1.57m/sec |
Cross Conveyor Operating Speed | 230 ft/min | 1.17m/sec |
Main Conveyor | 574″ x 48″ | 14580 x 1219mm |
Main Conveyor Operating Speed | 310 ft/min | 1.57m/sec |
Return Conveyor | 420″ x 24″ | 10668 x 610mm |
Return Conveyor Operaing Speed | 240 ft/min | 1.22m/sec |
POWER | ||
---|---|---|
HP | KW | |
Impact Crusher – Direct Drive | 250 | 187 |
Feeder | 30 | 22 |
Discharge Conveyor | 20 | 15 |
Return Conveyor | 10 | 7.5 |
Screen | 20 | 15 |
Pan Feeder | 2.5 | 2 |
Cross Conveyor | 5.5 | 4 |
Main Conveyor | 20 | 15 |
Magnet | 3 | 2 |
Diesel Cat C9.3B | 415 | 310 |
Generator | 235 | 175 |
TRANSPORTATION | ||
---|---|---|
LBS | KGS | |
Rear Axle | 81,064 | 36,770 |
King Pin | 46,295 | 20,999 |
TOTAL | 127,360 | 57,769 |