A massive shout-out to Eli Whitney Blake, an American inventor who created the primary jaw crusher in 1858. His early design is the foundation of modern jaw crushers. It is still used today, earning the title of oldest rock crusher on the planet.
Why has the jaw crusher stayed relatively unchanged? Its simple design is super effective at crushing almost anything, including the earth’s most challenging materials, like granite and iron ore. Also, it is easy to use and needs little maintenance, adding to the machine’s popularity.
One Job to Do
Primary jaw crushers’ reason for existence is to break down large rocks into smaller, manageable pieces. Why is it called primary? These crushers are used in the first phase of a crushing project or as the primary crusher on the job. They set the stage for further crushing and processing by providing a reliable, durable, and efficient first step in material handling.
How it Works
Let’s talk more about the simplicity of a jaw crusher. How it works is not complicated. There are two jaws—a moving jaw (or swing jaw) and a jaw that stays put. The moving jaw compresses the material against the stationary jaw, producing the crushing action.
Many primary jaw crushers are enormous and equipped with a massive feed opening, which determines the maximum material size that the crusher works with. They can handle giant rocks weighing several tons, perfect for jobs that start out with colossal materials that need breaking down.
Another key player in a jaw crusher is the toggle—a flat plate connecting the swing jaw to the crusher’s frame, amplifying its crushing force. Its role is to change the material’s rotational motion into a back-and-forth motion, causing the material to be crushed between the jaws.
What to Look for
A jaw crusher is a substantial investment, so getting the correct one to suit your needs is paramount. The pros at Lippmann can walk you through all the ins and outs to make sure your new crusher is spot-on.
Consider these features when making jaw crusher purchasing decisions:
- Capacity. The capacity of a jaw crusher is crucial because it controls the amount of material the crusher will process, usually measured in tons per hour. Matching the crusher’s capacity to the material’s hardness and the desired output size improves the crushing process by reducing backups and operational costs.
- Durability. A rock crusher needs to be durable, if nothing else. It works in unsympathetic environments, constantly dealing with abrasive materials and daily wear and tear. A durable rock crusher will perform without many breakdowns or the need for routine repairs, reducing downtime and maintenance costs while maximizing production.
- Energy Efficiency. Modern rock crusher designs take increased efficiency seriously. This is important because they focus on reducing operational costs by using less energy to break down rocks while curtailing ecological impacts. This means lower energy bills, cost-effectiveness, and, for the win, overall environmental sustainability.
Lippmann jaw crushers are built for demanding production, strength, and a lifetime of dependability. If you’re looking for a wheel-mounted portable jaw plant, a mobile jaw track plant, or a primary crushing station, we’ll work together to find you the perfect crusher. Check out Lippmann’s impressive lineup of jaw crushers, then connect with a local dealer who can answer all of your jaw crusher questions.
What Industries are Jaw Crushers Used Most?
- Construction. Reducing large rocks or demolition debris to be used in aggregate production.
- Mining. Breaking down ores for further processing.
- Quarries. Crushing large rocks into gravel or smaller sizes for construction materials.
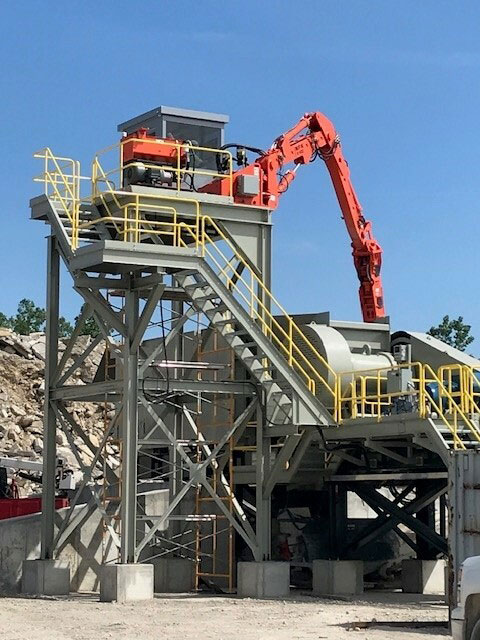
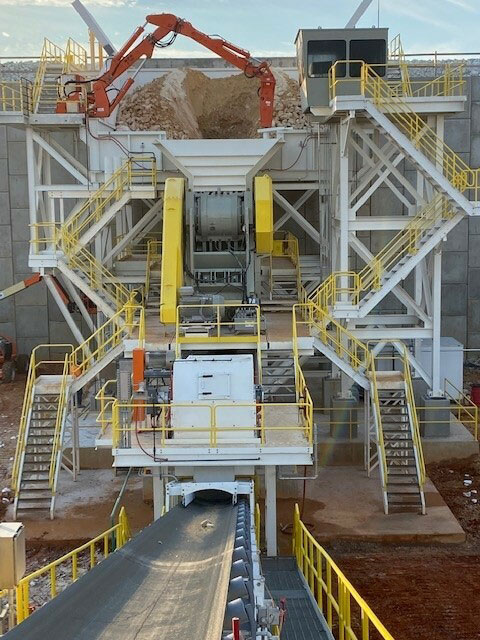